- Sensor and networking excellence for Packaging, Food, Beverage, Pharma, and Personal Care industries
- Life Science
- Drive Technology
- Automation in the semiconductor industry
- Steel and Metallurgical Industry
- Mobile Equipment
- Metalworking
- Advancing battery manufacturing automation: achieving superior efficiency and quality
- Automobile industry and suppliers
- Intralogistics automation: improve efficiency and throughput
- Plastic Industry
- Energy Production
- Fluid Power Technology
- White goods
- Electronics industry
- Tire Industry
- Traffic Engineering
Fluid Power Technology
For traditional use with digital IIoT-capable solutions
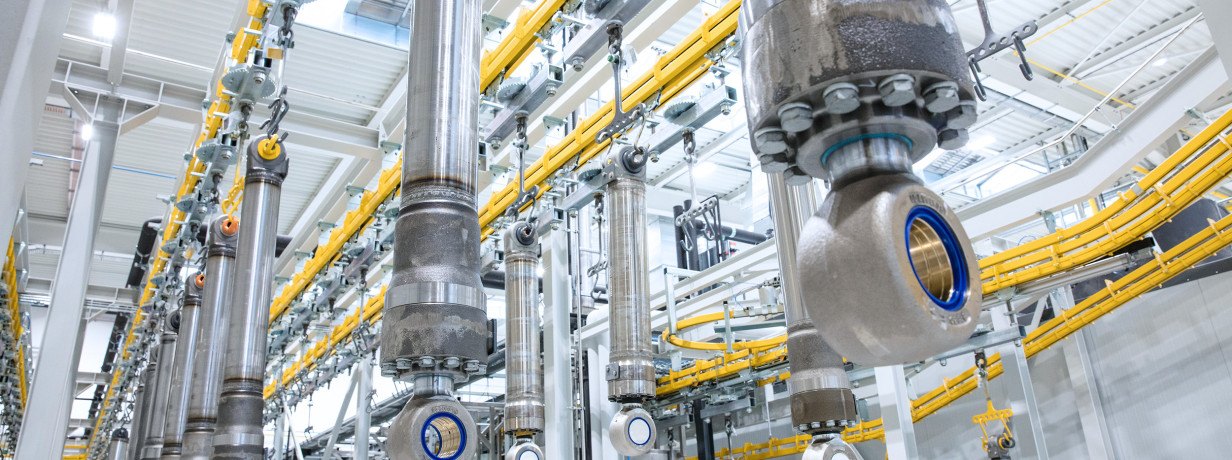
For your hydraulic and pneumatic systems Balluff offers innovative, state-of-the-art solutions. With various technologies for monitoring temperature, flow, level and travel as well as for intelligent position feedback, this wide range provides users with both process and service data. Whether you choose traditional solutions or wish to implement IIoT-capable applications, Balluff offers partnering support tailored to your needs from a single source.
The field of intelligent hydraulics is very broad, ranging from ultra-fast feedback in flight simulators or plastic injection molding machines to the harshest underground applications. But in energy production the watchword is high security. This is ensured by hydraulic systems using Balluff sensors, whether in blade adjustment for wind power systems or controlling steam valves on generators.
When assembly and automation technology calls for simple movements from A to B or gripping, holding, clamping or pressing in parts, pneumatic drive systems with Balluff position sensors are in demand. They stand out with simple topology construction, light and compact design and high energy efficiency, which is especially advantageous in holding or clamping applications such as on robotic grippers.
Detect Piston and Valve position in Hydraulics: For perfect integration in the pressure area
High pressure rated inductive sensors from Balluff are perfect for position monitoring of your hydraulics, for example, end-of-travel checking on hydraulic cylinders or monitoring valve positions. Installed directly in the pressure area, these sensors withstand pressures up to 500 bar.
And with a temperature range of up to 120 °C and a switching distance of up to 2.5 mm, they have universal application. Using the optional temperature output you can also protect the cylinder from overheating.
To handle position monitoring with non-magnetic cylinders, choose our universal magnetic field sensors.
Precise Feedback Systems Hydraulic Cylinders: Reliable position feedback offers security
When high reliability and precision are demanded, hydraulic drives with integrated magnetostrictive linear position sensors are the first choice. Directly installed in the pressure area of the hydraulic cylinder, this system ensures precise actual value detection of the piston position.
The various interfaces allow you to select the system that is right for your application. And stroke lengths of from 25 to 7500 mm cover every possibility. Our intelligent magnetic field positioning system is suitable for all non-magnetic cylinder types. This absolute positioning system continuously and highly accurately detects the current piston position through the cylinder wall. And it is easy to install, with no slot types to take into consideration.
The autonomous hydraulic compact drive: Energy efficiency and high positioning accuracy
Modern hydraulic compact drives, a union of hydraulics and electronics, are the combination of intelligence and power. This reduces installation and maintenance costs. And saves up to 80 % energy consumption by the axes.
The compact drive consists of a closed fluid circuit with cylinder, pump, control block and accumulator as well as the servomotor for the pump, the control unit with interface, and the sensors for monitoring pressure, temperature and travel. For integration in the closed fluid circuit of the compact drive, Balluff offers linear position sensors for reliable feedback to ensure high positioning accuracy. Also, Balluff offers compact intelligent sensors for pressure and temperature measurement. These report actual operating conditions and enable predictive maintenance. The data interfaces built into the drive – fieldbus, Ethernet, OPCUA or IO-Link – are used by the autonomous axis to communicate with the machine controller or directly to the cloud.
The intelligent pneumatic drive: IO-Link enables perfect linear feedback
Non-contact, wear-free magnetic field sensors for indicating end-of-travel and intermediate positions have long been a standard in pneumatic automation technology. They reliably detect the actual position in both pneumatically powered actuators such as cylinders and grippers and in special pneumatic applications such as on screwdrivers, maintenance units, motors, tensioners and slides.
Because of their capability of increasing digitalization of automation technology, more intelligent, networkable pneumatic actuators are in demand. For one thing, the piston travel needs to be continuously monitored so that automated position setting can be achieved. For another, it should be possible – beyond the actual process data – to obtain comprehensive service and diagnostics information. Our magnetic field positioning systems and sensors with IO-Link meet this specification completely. This intelligent technology provides all the desired data and ensures perfect linear feedback. It turns your pneumatic actuator into an optimal IIoT solution which moves you to the front row of digitalization in pneumatic drive technology.
Further information
Downloads
-
Sensors and Linear Position Sensors for use in a potentially explosive environment
-
Industry brochure fluid power technology