Rotary encoders: Precision positioning one rotation at a time
Explore the two main types of rotary encoders — incremental and absolute — and why you should choose one over another
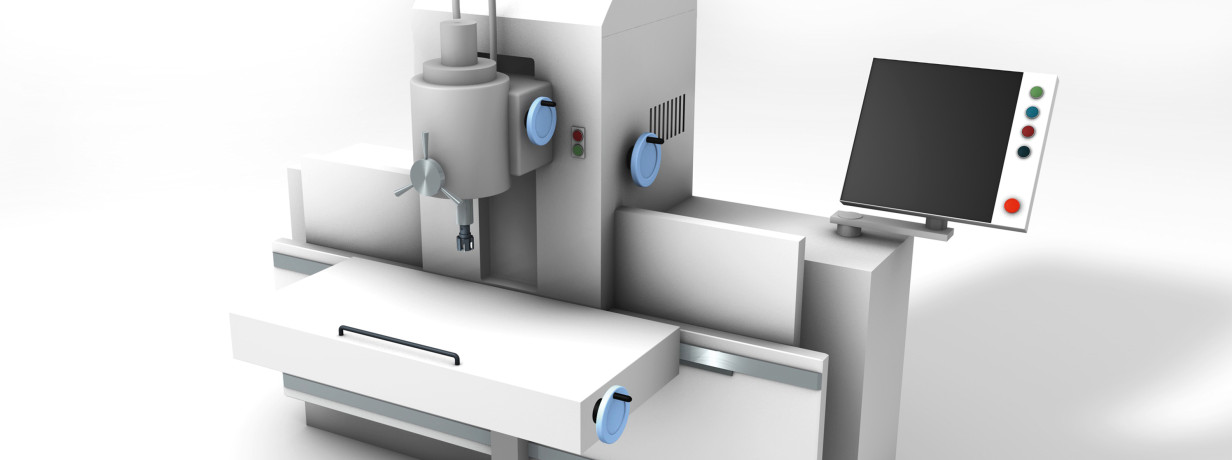
Reading Time: 3 minutes
Often, some of the most important automation sensors are the ones people know the least about or may not even realize they need for their applications. One of those sensors is the rotary encoder, which every industry uses to provide mechanical values for rotation angles and convert them into electrical signals to help you position all critical machine parts with high precision. The robustness of rotary encoders enables many uses even under extreme conditions, such as in food processing, machining processes, automotive component assembly, conveyor systems, and packaging equipment. Many vision systems in use today for inspection also require an encoder input for inspecting objects on the move.
The two main types of rotary encoders are incremental encoders and absolute encoders. Here’s a quick look at why you would choose one over another and some key characteristics.
Incremental encoder features
High-resolution angle measurement
High shaft load, up to 500 N
High protection classes for harsh environments, up to IP69K
Corrosion-resistant designs with stainless steel housings are available
Available interfaces, such as ABZ, sin/cos, TTL, and HTL
Optical technology for precise, high-resolution measurements or magnetic technology for use in harsh environmental conditions is available
Incremental encoders for speed monitoring and position determination
Incremental encoders compare machine data to the last data collection point and record it. Each time the machines and the encoder are switched on, they define reference values. Incremental encoders output a precisely defined number of pulses per revolution. The signal serves as a measure of the angle or distance covered. The more signals are output per revolution, the higher the resolution of the incremental encoders and the more precise the measurement and control of your system. With incremental encoders, you can monitor and reliably control the rotation and belt speed of your machines and systems. Some incremental encoder interfaces include ABZ, sin/cos, TTL (Transistor-Transistor Logic), and HTL (High Threshold Logic), which meet common and established industry interface requirements.
Absolute encoder features
Needs no homing run (they always know where they are)
No data loss in case of power failures
Corrosion-resistant designs with stainless steel housings are available
Robust design for harsh environmental conditions
Available interfaces, such as RS485, SSI, and CANopen
Available as single-turn or multi-turn encoder
Optical for precise, high-resolution measurements or magnetic for use in harsh environments
Absolute encoders for high-precision positioning and data acquisition
Absolute encoders detect positions and, unlike incremental encoders, assign a unique value to each signal. You know where your machines are at any moment, even during a power failure. Absolute encoders do not require a reference value or a homing run each time the machine is switched on, so your machine data is not lost to the encoder when switched off. You can monitor and reliably control the rotation and belt speed of your machines and systems. Some interfaces offered for absolute encoders include RS485, SSI, and CAN open, which meet common and established industry interface requirements.
Consideration for precision, robustness, and compatibility
When you start to configure either your incremental or absolute encoder for your application needs, there are some other characteristics to consider, such as single-turn or multi-turn for more precision. Optical or magnetic encoder for either high precision or robustness for harsh environments. The encoder housing needed standard or stainless steel for wash-down areas. For your mechanical connection point, you will need to determine your shaft diameter and flange style. These may seem like a lot of options, but encoder manufacturers offer simple selection guides to ensure you choose exactly what you need for your application.
As you become more aware of the many different types of automation products, don’t forget the rotary encoder if you need some precise positioning or speed measurement on your next application.
Keywords
- Sensor technology
Author
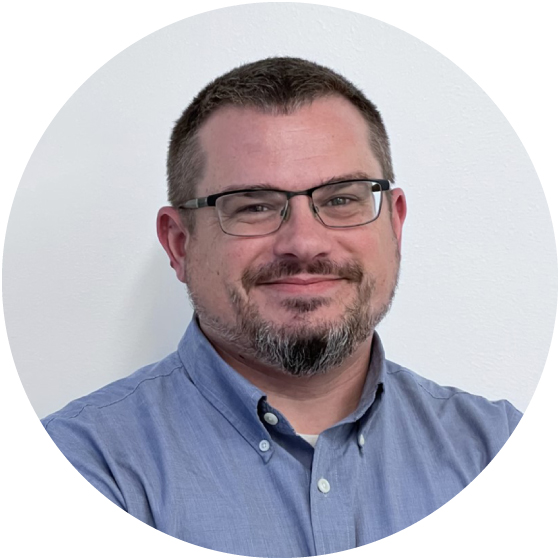
Jonathan Esposito
2 Contributions
Comment
Popular posts
Industrial sensing fundamentals – NPN vs PNP
What is a capacitive sensor?
How do I wire my 3-wire sensors?
The basic operating principle of an inductive proximity sensor
Contact form
Do you have any questions or suggestions? We are at your disposal.
Balluff Inc.
-
8125 Holton Dr.
Florence, KY 41042