- Magnetostrictive linear position sensors for explosive areas
- Magnetostrictive linear position sensors for extreme environments
- Magnetostrictive linear position sensors in profile housing
- Magnetostrictive position measuring systems for long distances
- Magnetostrictive position measuring systems for mobile hydraulics
- Redundant magnetostrictive linear position sensors
Magnetostrictive linear position sensors for industrial hydraulics
Magnetostrictive sensors
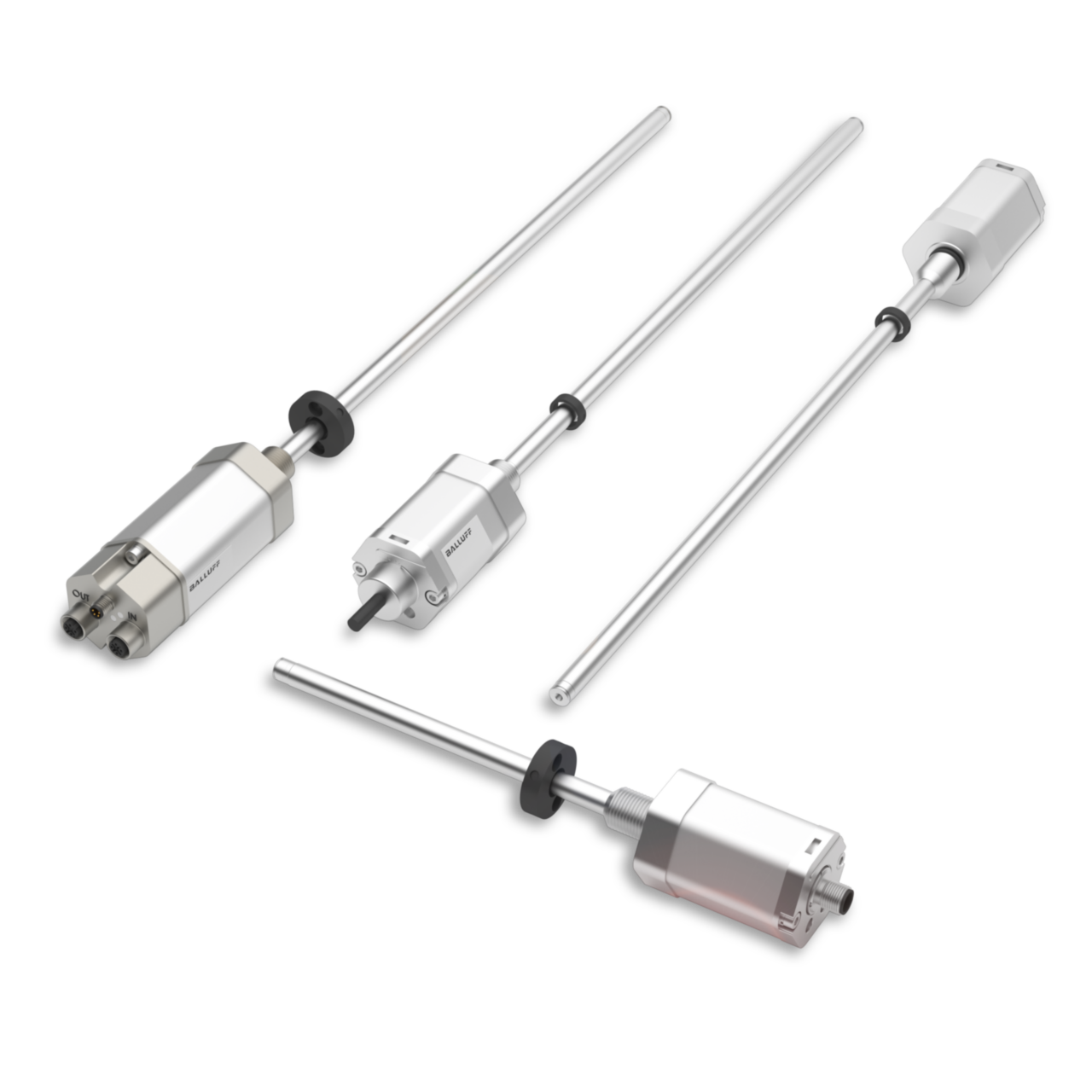
Available in:
25 versions
The most important application for our BTL magnetostrictive linear position sensors in rod design is in hydraulic drive units. They are exceptionally well-suited for use in hydraulic cylinders for position feedback, for molding and rolling mills, or for elevator and hoisting technology.
Since the sensors are installed in the pressure area of hydraulic cylinders, they have to have the same pressure resistance as the cylinder itself. The measurement element is installed in a pressure-rated tube made of non-magnetic stainless steel. The flange seals the high pressure area using an O-ring. Moreover, the electronics are integrated in a protective housing outside of the cylinder on the flange of the rod.
Features
- High resolution of up to 1 µm
- Measuring lengths of up to 7620 mm
- Measures several positions and speeds at the same time
- Programmable output signals – invert, configure, and document the measurement range
- Flexible installation thanks to various thread types
- Non-contacting, thus free from wear – no downtimes and a long service life
- Expanded measuring possibilities with multi-magnet technology
- Easy integration with equipment through a variety of interfaces – such as IO-Link, Profinet, EtherCAT, SSI, and analog
25 versions
Order code | Interface | Measuring length | Mechanical configuration | Ambient temperature | Linearity deviation | Application | Actions |
---|---|---|---|---|---|---|---|
![]() BTL C1 - Stab BN/ZN - IO-LinkBTL C1 - Stab BN/ZN - IO-Link |
IO-Link | 25...4000 mm |
a = B: fastening M18 thread a = Z: fastening 3/4 inch thread |
-40...85 °C | ± 50 µm | Hydraulic cylinder | |
![]() BTL B1 - Stab BN/ZN - AnalogBTL B1 - Stab BN/ZN - Analog |
k = A, 1: Analog, voltage k = E, 5: Analog, current |
25...4000 mm |
a = B: fastening M18 thread a = Z: fastening 3/4 inch thread |
-40...75 °C |
nnnn = 0050…0500: ± 200 µm nnnn > 0500: ± 0.04% FS |
Hydraulic cylinder | |
![]() BTL C1 - Stab BN/ZN - AnalogBTL C1 - Stab BN/ZN - Analog |
k = A, 1: Analog, voltage k = E, 5: Analog, current |
25...4000 mm |
a = B: fastening M18 thread a = Z: fastening 3/4 inch thread |
-40...85 °C |
nnnn = 0050…0500: ± 60 µm nnnn ≥ 0500: ± 0.012% FS |
Hydraulic cylinder | |
![]() BTL7 -Y/Z- Series - DigitalBTL7 -Y/Z- Series - Digital |
Digital pulse | 25...7620 mm | Fastening 3/4" threads | -40...85 °C | nnnn = 0025…5500: ± 50 µm, nnnn > 5500: ± 0.02% FS | Hydraulic cylinder | |
![]() BTL7 -Y/Z- Series - EtherCATBTL7 -Y/Z- Series - EtherCAT |
EtherCAT | 25...7620 mm | Fastening 3/4" threads | -40...85 °C | nnnn = 0050…5500: ± 30 µm, nnnn > 5500: ± 0.02% FS | Hydraulic cylinder | |
![]() BTL7 -Y/Z- Series - EtherNet/IPBTL7 -Y/Z- Series - EtherNet/IP |
EtherNet/IP | 25...7620 mm | Fastening 3/4" threads | -40...85 °C | nnnn = 0050…5500: ± 30 µm, nnnn > 5500: ± 0.02% FS | Hydraulic cylinder | |
![]() BTL7 -Y/Z- Series - ProfinetBTL7 -Y/Z- Series - Profinet |
Profinet | 25...7620 mm | Fastening 3/4" threads | -40...85 °C | nnnn = 0050…5500: ± 30 µm, nnnn > 5500: ± 0.02% FS | Hydraulic cylinder | |
![]() BTL7 -Y/Z- Series - Analog VoltageBTL7 -Y/Z- Series - Analog Voltage |
Analog, voltage | 25...7620 mm | Fastening 3/4" threads | -40...85 °C | nnnn = 0050…0500: ± 50 µm, nnnn = 0501…5500: ± 0.01% FS, nnnn > 5500: ± 0.02% FS | Hydraulic cylinder | |
![]() BTL7 -Y/Z- Series - SSIBTL7 -Y/Z- Series - SSI |
SSI | 25...7620 mm | Fastening 3/4" threads | -40...85 °C |
d = 1, 2, 3, 7: nnnn = 25…5500: ± 30µm d = 4, 5, 6, 8 nnnn = 25…5500: ± 2 LSB nnnn > 5500: ± 0.02% FS |
Hydraulic cylinder | |
![]() BTL7 -Y/Z- Series - Analog CurrentBTL7 -Y/Z- Series - Analog Current |
Analog, current | 25...7620 mm | Fastening 3/4" threads | -40...85 °C | nnnn = 0050…0500: ± 50 µm, nnnn = 0501…5500: ± 0.01% FS, nnnn > 5500: ± 0.02% FS | Hydraulic cylinder |
Edit columns
Please select which columns should be displayed.