- Sensor and networking excellence for Packaging, Food, Beverage, Pharma, and Personal Care industries
- Advancing battery manufacturing automation: achieving superior efficiency and quality
- Automobile industry and suppliers
- Steel and Metallurgical Industry
- Automation in the semiconductor industry
- Life Science
- Metalworking
- Plastic Industry
- Fluid Power Technology
- Mobile Equipment
- Energy Production
- Intralogistics automation: improve efficiency and throughput
- Drive Technology
- White goods
- Electronics industry
- Tire Industry
- Traffic Engineering
Optimizing electrode manufacturing for superior battery performance
Utilizing advanced solutions for slurry mixing, coating, drying, and calendering
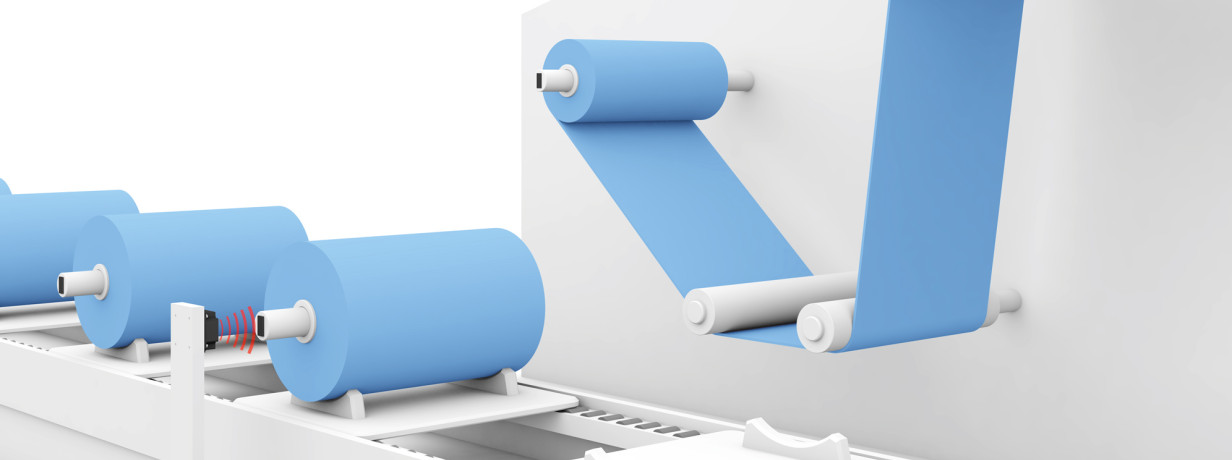
Electrode manufacturing is critical for lithium-ion battery quality and performance. This process encompasses slurry mixing, coating, drying, and calendering, each presenting unique challenges such as consistency and cycle time optimization.
Balluff offers specialized solutions like RFID systems for traceability, optoelectronic sensors for quality control, and IO-Link technology for cost-efficient device communication, collectively enhancing consistency, product quality, and Overall Equipment Efficiency (OEE) in battery manufacturing.
Integrating our technologies into your electrode manufacturing process allows for superior quality and efficiency, laying the foundation for enhanced battery performance. Our solutions are designed to ensure precise slurry mixing, consistent coating, and optimized drying and calendering processes, delivering tangible results.
Spotlight applications in electrode manufacturing
Discover applications where our technology ensures precision and quality, enabling you to focus on what really matters: optimizing your production efficiency.
Transform electrode production with best of class products
Unlock a new level of precision and control in your electrode manufacturing operations with our targeted solutions, proven-in-use by leading battery producers and machine builders.
Explore more in battery manufacturing
Discover how Balluff’s solutions can improve other key areas of your battery manufacturing process.
Questions? Ask our experts!
Expand your knowledge
Downloads
-
Industry brochure battery industry