Rotary encoder
For controlling, measuring and monitoring rotary movements
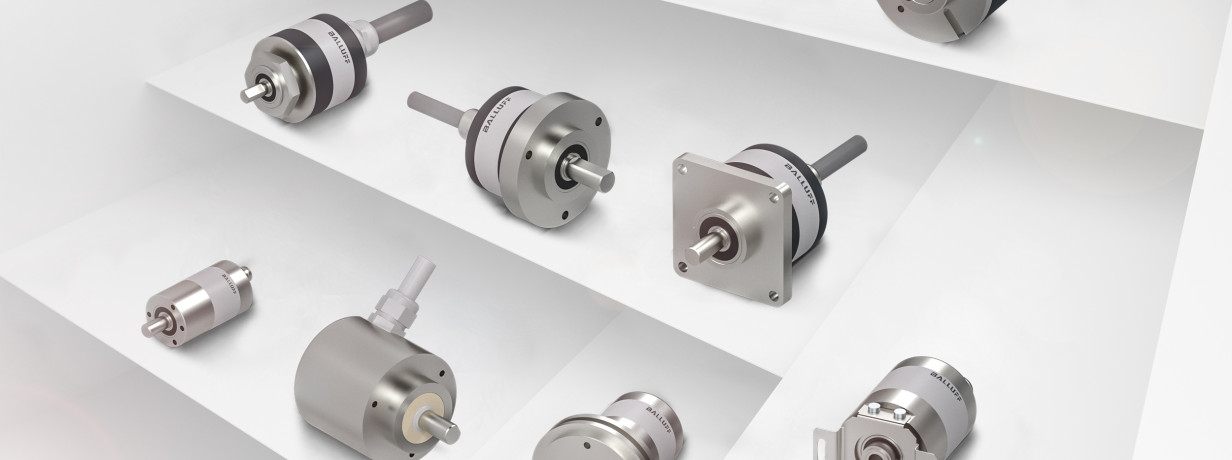
Balluff's encoders are used wherever mechanical values for angles of rotation need to be captured. The detected movement is converted into electrical signals to help you to position all critical machine parts with high precision. The robustness of the rotary encoders enables use even under extreme conditions, such as in the field of food processing and packaging, mobile working machines as well as in mechanical engineering. Here you can find the right encoder for your applications, whether as an absolute encoder or as an incremental encoder.

Incremental encoders
- High-resolution angle measurement
- High shaft load up to 500 N
- High protection classes up to IP69K
- Corrosion-resistant design with stainless steel housing
- Available interfaces, among others: ABZ, sin/cos, TTL, HTL
- Optical technology for precise, high-resolution measurements or magnetic technology for use in harsh environmental conditions available
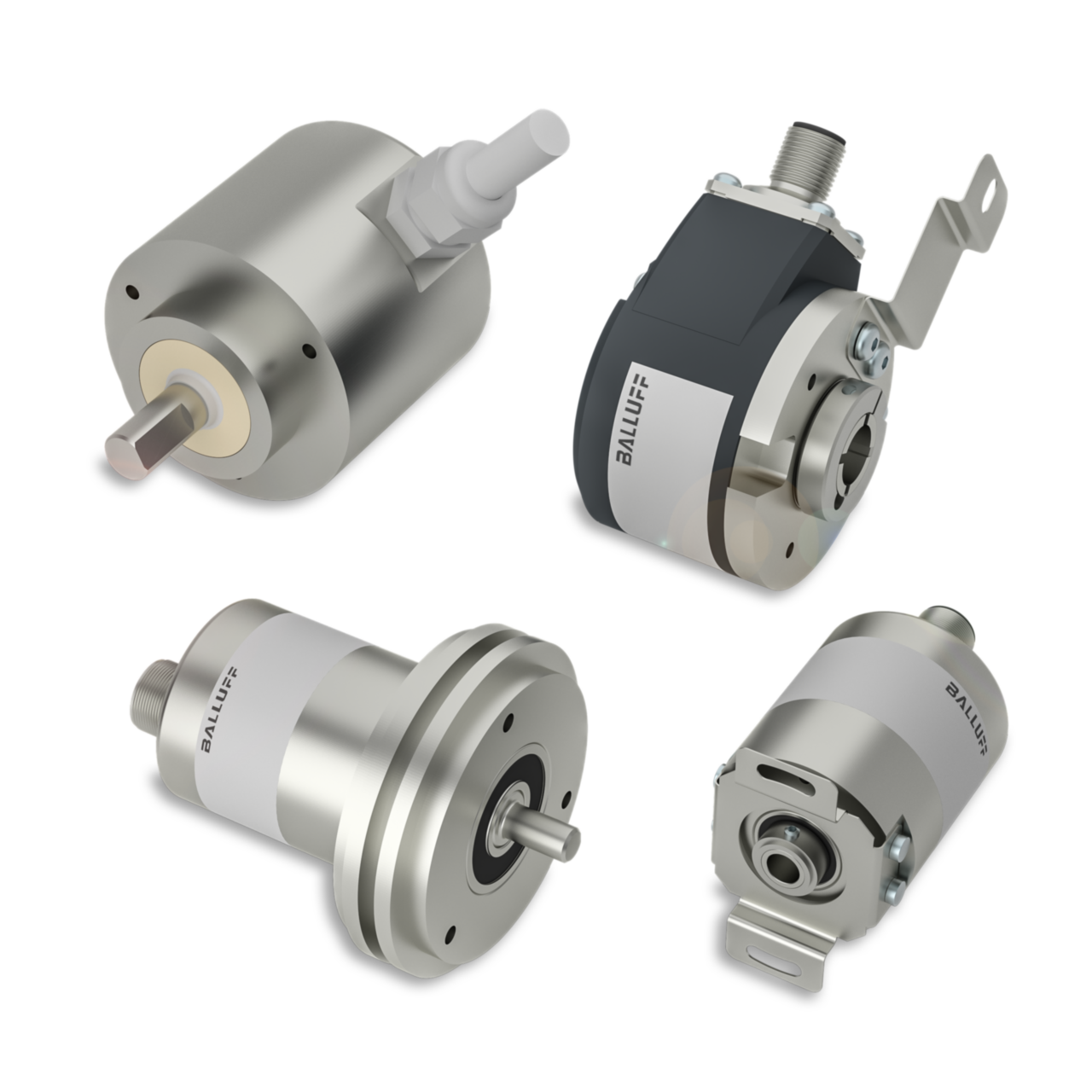
Absolute encoders
- Needs no homing run
- No data loss in case of power failures
- Corrosion resistant design with stainless steel housing
- Robust design for harsh environmental conditions
- Available interfaces, among others: RS485, SSI, CANopen
- Available as single-turn or multi-turn encoder
- Optical for precise, high-resolution measurements or magnetic for use in harsh environments
Incremental encoders for speed monitoring and position determination of your machines and systems
Incremental encoders record machine data in comparison to the last data collection. For this purpose, reference values are defined each time the machines - and thus also the sensors - are switched on. Incremental encoders output a precisely defined number of pulses per revolution. The signal serves as a measure of the angle or distance covered. The more signals are output per revolution, the higher the resolution of the incremental encoders and the more precise the measurement and control of your production systems. With our incremental encoders, you monitor and reliably control the rotation and belt speed of your machines and systems, but you can also use them for high-resolution angle measurement. Incremental encoder interfaces include ABZ, sin/cos, TTL (Transistor-Transistor Logic) and HTL (High Threshold Logic), which meet common and established industry interface requirements.
Overview of key features and benefits of the incremental encoder
- Angle measurement with high resolution
- Applications with high shaft load up to 500 N
- High protection classes up to IP69K
- Corrosion resistant version with stainless steel housing available
- Available interfaces of the incremental encoders, among others: ABZ, sin/cos, TTL, HTL
Absolute encoders for all your positioning needs: High-precision positioning and reliable data acquisition
Absolute encoders detect positions and, unlike incremental encoders, assign a unique angular position or a unique value to each signal. With our absolute encoders, you know where your machines are at any moment, even in the event of a power failure. Absolute encoders do not require a reference value or a reference run each time the machine is switched on, so your machine data is not lost to the encoder when it is switched off. The interfaces of the absolute encoders include RS485, SSI and CAN open.
Overview of key features and benefits of absolute encoders
- Encoder does not need homing unlike incremental encoders
- Reliability: No data loss in case of power failures
- Corrosion resistant design with stainless steel housing available
- Rugged design of encoders for harsh environmental conditions
- Available interfaces of the absolute encoders, among others: RS485, SSI, CANopen
Multi-turn encoder vs. single-turn encoder
With single-turn encoders, the coded output signals are repeated with each new revolution of the shaft. Single-turn encoders have a measuring range of 360 degrees, i.e. exactly one revolution. If the shaft is rotated more than 360 degrees, the output parameters of the further revolutions correspond again to the signal of the first revolution. Without additional data processing or corresponding evaluation or monitoring of the output signal, it is therefore not possible to sum the complete revolutions already made using individual data points with the single-turn encoder.
Multi-turn encoders, on the other hand, enable the measurement of a range of more than 360 degrees. The encoders can thus generate a distinctive output signal for each shaft position for over 8 trillion revolutions. The output signal from the encoders is determined by the number of revolutions and the shaft position within a revolution and is unique within the signal variance of the maximum 8.8 trillion revolutions. This enables a valid and reliable record of the revolutions of the encoder already completed.
Optical encoder: Highest resolution and precision due to our optical measuring principle
Optical rotary encoders are sensors that use an optical measuring principle to operate very precisely with the highest image resolution and generate digital pulses. An optical encoder consists of a transparent code disk that is illuminated by an LED and converts the received data into electrical signals. The optical measuring principle enables the highest precision in data acquisition.
Magnetic encoders: The robust solution for harsh working environments
Magnetic encoders from Balluff are particularly suitable for use in harsh environmental conditions such as extreme temperatures. They are insensitive to shock and vibration and are an all-round robust solution among encoders for applications in heavy industry or machine tools. There are no limits to the areas of application, because the compact design enables use even in the smallest machine parts.
Put together the encoder that is right for you with our encoder configurator
With the help of our encoder configurator, you can quickly and easily find the perfect encoder for your application from 1.8 million variants. Whether incremental or absolute, magnetic or optical, our encoders fit your requirements.
Licensing declaration
The following open source components are used: eCos V3.0
Source: http://ecos.sourceware.org/
License: eCOS license