04.07.2023
Innovation meets miniaturization
At the center of excellence at the Neubiberg site near Munich, Germany, Balluff collaborates with its customers to design highly precise smart photoelectric measuring systems for a wide range of IIoT applications.
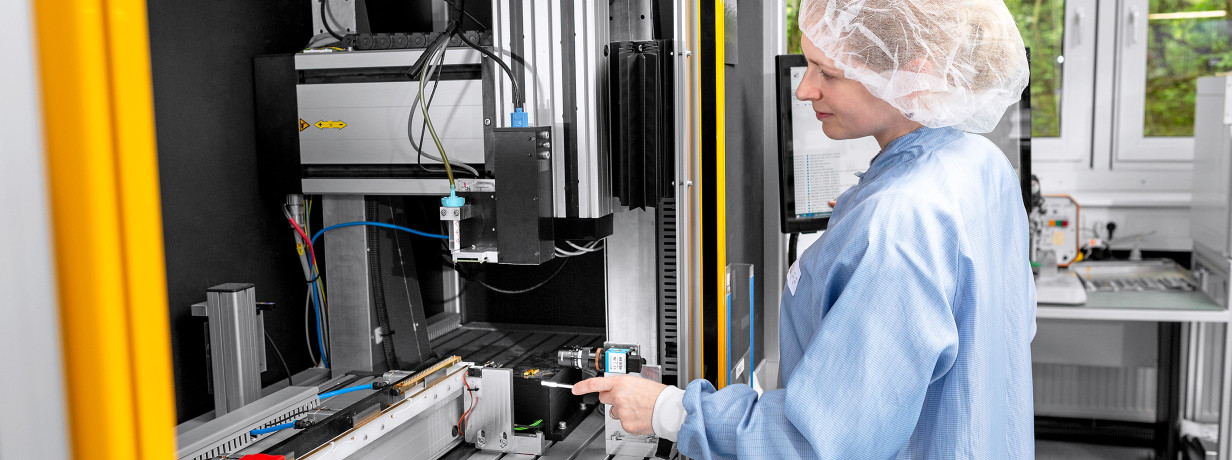
1989 was the year of new beginnings and far-reaching change. The company Sensor Technologie München GmbH (STM) from Neubiberg in the German state of Bavaria was founded as an affiliate at the University of the Bundeswehr, the German Armed Forces. Its purpose was to offer photoelectric sensors with extremely small frame sizes, something that did not exist back then. Extremely small in this case meant LED chips with edge lengths of only 0.3 to 0.4 mm in small housings 2 mm in diameter or with M3 screw connections. Edgar Melzner had developed a technology together with Professor Hans-Dieter Ließ in which LEDs and photodiodes made of sawn wafers are placed together with a sleeve on special carries. By means of a patented process, a lens made of optical epoxy resin is cast directly onto it. The result: specialty sensors. This process, which has since been further developed, is still considered groundbreaking on the market today.
From development partnership to integration
Due to its unique product portfolio, STM and its 50 employees became a part of the Balluff group in 2014. The two companies had previously already worked together in a development partnership. In late 2020, STM founder Edgar Melzner retired as a site manager after very successful years of growth. His successor Dr. Michael Greif is set to turn the location into a center of excellence. Today, more than 100 employees produce both customer-specific optical sensors and standard opitcal products for a wide range of industrial applications. Dr. Michael Greif has dedicated himself to the goal of structurally adapting the site to the strong growth while at the same time maintaining its innovative strength. Even today, many new product ideas are bubbling up from the center of excellence in Munich.
As such, Balluff Munich focuses on further developing technologies within the Balluff Group. With its many years of expertise and customer-focused development, the site ideally complements the production and logistics network, driving innovative solutions and supporting the launch of new products.
Site manager Dr. Michael Greif is developing Balluff Munich as a competence center.
Committed to developmental engineering
Dr. Florian Furtmayr, Head of R&D, summarizes why the process is so special: “We don’t start off with LED modules already in their housing, but with chips made from cut wafer elements which we purchase. We carry out the customized design and manufacturing by ourselves.” This also includes the necessary amplifying units from different technology generations. Dr. Florian Furtmayr is a committed physicist and loves new challenges. The high level of development and production depth at the Balluff Munich site makes this possible.
Display of the production machine during the lens encapsulation process for LED production
Modular set-up for a greater freedom of choice
A modular set-up ensures that the sensor heads can be combined with the other technology modules as required. Thanks to the variable optic, the customer can choose any suitable source of light. “This includes, for example, red light in the 650 nm range or in the near-infrared range of 1,480 or 1,550 nm. The latter two wavelengths are absorbed by water, which makes it easier to measure liquids.
This is particularly interesting for our customers in laboratory automation and the pharmaceutical industry. They have to analyze watery substances like blood, which our customized optical sensors are ideally equipped to do,” says site manager Dr. Michael Greif. The physicist, who holds a doctorate, knows what he is talking about, having already dealt intensively with tricky questions in optics in his doctoral thesis. He has been generating many creative ideas at the Munich site for eight years.
Room for configurations
In addition to the optical sensor head, an amplifier, or processor respectively, are necessary. It is a closed system which communicates with a backend to visualize results using a control unit or IO-Link. “We offer the customer much room for their own configurations, like concerning the chip power and position, lens geometry, amplifier unit and housing design, combined with the desired cable length," explains the physicist.
Listening closely
The project collaboration is only completed when the customer has been provided a solution that precisely meets their requirements. “This mostly involves questions about the application geometry: Does it reflect or transmit light? And which light wavelength is to be used? The type of signal processing also plays a central role in solving the measurement task," adds the site manager.
”Speed matters” as a guiding principle
Modern simulation methods such as ray tracing and evaluating light spots in real time help the development teams to land on a suitable design faster. Thanks to the use of 3D printing in prototype development, results can be discussed with customers within days instead of months. At the laboratory, the customer's configuration is recreated to track down the best combination of transmitter and receiver. Depending on the requirements, recommendations are made for the best suited amplifier setting or customized amplifiers are developed instead.
About half of the approximately 230 different sensor heads, which originate from the development of Balluff Munich and are manufactured in self-developed, highly specialized machines, can be purchased as catalog goods via the Balluff webshop. The rest are customer-specific solutions. And demand for the latter has skyrocketed in recent years. This is why a special sales department was created to cover this Customer Defined Engineering (CDE), approaching potential customers and discussing their issues in an expert manner. For example: If properties such as vacuum resistance are required, then PEEK would be a suitable material for the housing. Or should it rather be one made of Teflon? “We are constantly operating in the gray area between CDE and standard products,” says Christiane Maier, Product Cluster Manager “Photoelectric Sensors”, who, as an outspoken analyst, does not lose sight of business despite the strong “customer first” focus.
Advanced simulation techniques such as ray tracing accelerate design discovery for development teams.
Balluff Product Cluster Photoelectric Sensors
There are two Balluff sites that develop highly precise photoelectric miniature sensors (“Product Cluster Photoelectric Sensors“): the headquarters in Neuhausen as well as Neubiberg near Munich. The product manager provides guidance: “Core strengths of the Munich site are short-cycle thinking and agile, customer-oriented development methods. The ideal combination of the production network with sites in Chengdu and Veszprém and, in the future, Aquascalientes with its processes geared to high-volume product classes and the customer-specific detail work in the centers of excellence such as Neuhausen or Neubiberg are what make Balluff so strong."