Precision gear system assembly line for the manufacture of residential water meter mechanisms
Case Study
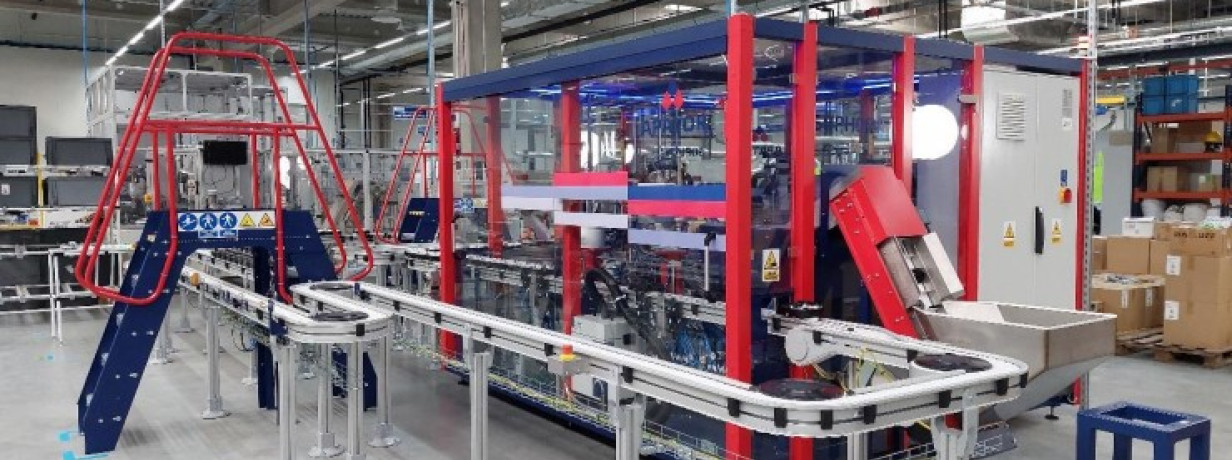
Reading Time: minutes
Apator Powogaz SA a leader in the production of water meters, faced challenges in the precise assembly of the complex gear systems contained in the mechanism of residential water meters. The manual process of assembling these parts was time-consuming, labour-intensive, error-prone and limited production efficiency.
The company needed an innovative solution to automate assembly, reduce production time, increase productivity, eliminate errors and maintain the highest quality of water meters.
Apator Powogaz is the world's leading manufacturer of water meters. It has more than 100 years of experience in the production of water meters, heat meters and heat cost allocators. The company specialises in remote consumption reading, billing and management of water and heat distribution systems. With its state-of-the-art factory and a team of 400 employees, Apator Powogaz operates in more than 60 export markets, with planned revenue for this year at 350 million zlotys. In the water meter segment alone, it has as much as 50% share on the Polish market and 7% share on the European market.
Situation
The process of assembling the gear system of the water meter mechanism involved assembling many different small mechanical parts, more than 20 types of gears in total, including some equipped with neodymium magnets. Each of these mechanisms consisted of an upper white disc and a lower black disc, which also came in different variations and designs, further complicating the whole process. Such diverse components required precision and accuracy in monitoring the flow of water passing through the water meter and the company needed an efficient solution to meet this demanding challenge.
Prior to the automation of the gear assembly the process was done manually, this not only made the process inefficient but also prone to errors and manufacturing defects creating difficulties in ensuring production continuity and assembly precision. These quality issues and the cost of manual labour put a significant strain on the company's budget.
Problem
Apator Powogaz decided to optimise the production process to reduce manual labour, improve quality assurance processes and lower manufacturing costs. This was a huge investment and challenge as it was necessary to create a complex and innovative solutions for the automatic assembly of the gear mechanism of the water meters.
Within this complex gear mechanism there are a large number of different configurations, up to 70 different variants, each tailored to meet specific application requirements. A wide range of configurations and components were required to be assembled with great precision.
Solution
In response to the manufacturer's needs, the Robotisation and Automation Department of the Apator Group developed an advanced machine for the automatic assembly of the gear mechanism. The machine was designed to ensure maximum precision, efficiency and quality of assembly.
The Robotisation and Automation Department engineers proposed a solution based on an indexing rotary table with an industrial assembly robot. The automated assembly line was to use state-of-the-art robotics and vision systems to meet the specific requirements of assembling the gear mechanism.
The rotary table houses universal sockets so that different product designs can go into the same socket. Each socket is precisely designed to fit perfectly into the corresponding components. This allows for high repeatability and accuracy in assembly.
The process uses five vibration feeders to precisely feed successive components for assembly. Five advanced assembly robots each programmed to perform various assembly operations. The robots provide accurate positioning and pressure to ensure that components are assembled in a repeatable manner and in accordance with design specifications.
In addition, a number of Balluff sensors (560 different parts in total) have been used, which are responsible for continuous quality control during assembly. These systems accurately analyse the position and colour of the parts to detect even the smallest deviations, so that potential problems can be addressed immediately.
How it works.
The process begins with the retrieval of semi-finished parts from transport pallets located on conveyors. Balluff's vision system then verifies the correct functioning of the mechanism by checking the alignment of gears and drums at specific positions. After positive verification, the half-finished product goes to the rotary table where the next component is added. Thanks to precisely designed sockets, the components are accurately positioned under the robots and assembled with to a high tolerance. The entire assembly process takes only 8 seconds and the robots work in harmony to ensure the smooth flow of semi-finished products through the production line. The final product is individually numbered using a laser marker, allowing each water meter to be tracked throughout its lifetime. This also makes it easier to identify in case of any problems, which is crucial to maintaining excellent product quality.
Accurate machine operation:
The process begins by taking a half-finished product (white disc assembly) from dedicated transport pallets and placing it on a special two-position rotary table.
A vision camera scans the semi-finished product identifying the correct position of the pinions and drums relative to each other to ensure precise and accurate measurement of water flow through the water meter.
The white disc assembly is securely mounted in the product cavity on a rotary table to ensure precise and repeatable placement.
Industrial assembly robots at successive stations assemble the appropriate gears, carefully inserting a 1.7-millimetre-diameter pin into the 1.8-millimetre-diameter hole of the white disc.
A vision camera scans the pre-assembled gear mechanism, identifying the proper mesh and position of the components.
The black disc is securely seated in the gear mechanism, and a dedicated proprietary circuit simulates the flow of the medium and ensures that the assembly is correct.
The finished product is encased in a sealed enclosure where laser marking takes place to maintain full traceability.
The entire process takes just a few seconds, which means that every 8-9 seconds another complete and precisely mounted water meter comes off the production line.
Customer benefits
Thanks to the implementation of the innovative solution for automating the assembly of the gear mechanisms, Apator Powogaz SA has recorded a number of key benefits:
-
Precision and repeatability.The use of advanced robots as well as vision and sensor systems allowed to maintain high precision and repeatability of the assembly, eliminating manufacturing errors and defects.
-
Cost reduction and increased productivity.Automation of the process has resulted in a significant reduction in costs resulting in higher production efficiency. The machine operates 24/7 without the need for rest breaks or manning changes, further increasing productivity. Thanks to the fast and precise installation of water meters the company is able to meet higher product demand and increase their profitability.
-
Elimination of errors and complaints.The automated assembly process has ensured significantly fewer production errors leading to defective finished units. As a result, the number of returns from customers has been significantly reduced.
-
Reduction in production costs and time.Manual assembly of the water meter gear mechanism took a lot of time and was more labour-intensive. With automation, production time was significantly reduced, enabling the manufacturer to deliver water meters to the market faster.
-
Multifunctionality and flexibility.The use of a rotary table and programmable robots made it easy to adapt the production line to different types of water meters. The control system makes it possible to quickly and automatically changeover the line to adapt to a different type of water meter, without long downtimes and errors during the changeover process. This enables the company to respond quickly to changes in the market and customer demand, giving it a competitive advantage.
-
Monitoring and quality controls.Thanks to Balluff's solutions, each water meter is subjected to detailed quality control at every stage of assembly. This makes it possible to detect even the smallest defects and respond immediately, resulting in the delivery of only the highest quality products to customers.
Designed by the Robotisation and Automation Department of the Apator Group, the precise machine for assembling the gear mechanism of water meters is an innovative solution that has completely changed the production process in the company. The implementation of the new automatic machine was a milestone for the company, as it led to a remarkable achievement in high precision. This has allowed the manufacturer to reduce production time, increase productivity, eliminate assembly errors and provide customers with products of the highest quality. The automation of this process is an example of how advanced technologies can significantly contribute to a company's success in a competitive market.
About the company
Grupa Apator is a respected manufacturer of advanced technical solutions based in Poland, which specialises in the production of water meters, electricity meters, as well as in offering comprehensive industrial automation systems. Its R&D department is a team of qualified engineers and specialists who constantly seek innovative solutions and improve products to meet the demands of a dynamic market.
Keywords
- Case Study
- Efficient production
- Innovations
Author
We have been active on the Polish market for more than 25 years. We serve our customers from Pomerania to the Tatra Mountains, providing first-class service and technical support. We are also present online, where we share our knowledge about the latest implementations, industry trends, events or technical aspects of our solutions.
17 Contributions
Comment
Popular posts
Advantages of inductive proximity sensors in industry
BCM - a sensor that detects anomalies
Optoelectronic sensor
Precision gear system assembly line for the manufacture of residential water meter mechanisms
Contact form
Do you have any questions or suggestions? We are at your disposal.
Balluff Limited
-
20 Cheshire Business Park
Cheshire Avenue
Lostock Gralam
Northwich, CW9 7UA