- Life Science
- Automation in the semiconductor industry
- Steel and Metallurgical Industry
- Drive Technology
- Metalworking
- Mobile Equipment
- Sensor and networking excellence for Packaging, Food, Beverage, Pharma, and Personal Care industries
- Advancing battery manufacturing automation: achieving superior efficiency and quality
- Automobile industry and suppliers
- Fluid Power Technology
- Plastic Industry
- Intralogistics automation: improve efficiency and throughput
- Energy Production
- White goods
- Electronics industry
- Tire Industry
- Traffic Engineering
Advancing battery manufacturing automation: achieving superior efficiency and quality
Empowering producers to meet the evolving demands of the electric vehicle market
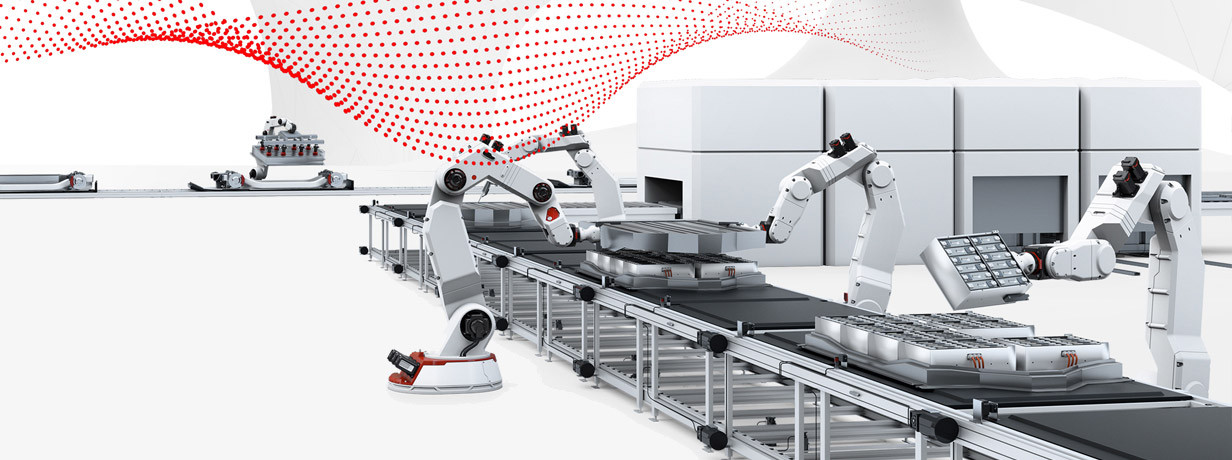
The rise of electric mobility and the growing demand for efficient energy storage are pushing lithium-ion batteries to the forefront of technological innovation. As your strategic partner in this dynamic industry, Balluff empowers machine builders, automakers, and battery manufacturers to navigate these complexities with confidence.
We offer a diverse suite of products and solutions, each tailored to meet the unique challenges at every key stage of battery manufacturing. From electrode manufacturing and battery cell assembly to cell finishing to module and pack assembly, we provide components that address your specific needs in cycle time, traceability, and quality control. The result? Enhanced Overall Equipment Efficiency (OEE) and a production process that's not just cost-efficient, but also future-ready.
Take advantage of cutting-edge solutions and technologies like IO-Link, condition monitoring, smart sensors, RFID, and vision systems to gain data-driven insights for impeccable product quality and peak operational efficiency. With Balluff by your side, you're not just keeping pace with industry advancements—you’re leading the way.
Free webinar
Enhancing battery manufacturing efficiencyElevate your operations in key battery manufacturing areas
Discover how Balluff's solutions can revolutionize each critical phase of your battery manufacturing process.
Spotlight applications in battery manufacturing
Learn about select applications that offer insights into how we tackle specific challenges within battery manufacturing, bringing transparency and efficiency to your machines to maximize OEE.
Optimize your battery manufacturing with our proven solutions
Discover a range of specialized products designed to tackle the unique challenges in battery manufacturing. From condition monitoring to advanced traceability, our products help you boost your OEE and ensure production quality.
Questions? Ask our experts!
Expand your knowledge
Downloads
-
Industry brochure battery industry