- Sensor and networking excellence for Packaging, Food, Beverage, Pharma, and Personal Care industries
- Drive Technology
- Steel and Metallurgical Industry
- Fluid Power Technology
- Automation in the semiconductor industry
- Life Science
- Metalworking
- Mobile Equipment
- Plastic Industry
- Automobile industry and suppliers
- Intralogistics automation: improve efficiency and throughput
- Energy Production
- White goods
- Electronics industry
- Advancing battery manufacturing automation: achieving superior efficiency and quality
- Tire Industry
- Traffic Engineering
Drive Technology
Increase energy efficiency – Improve quality
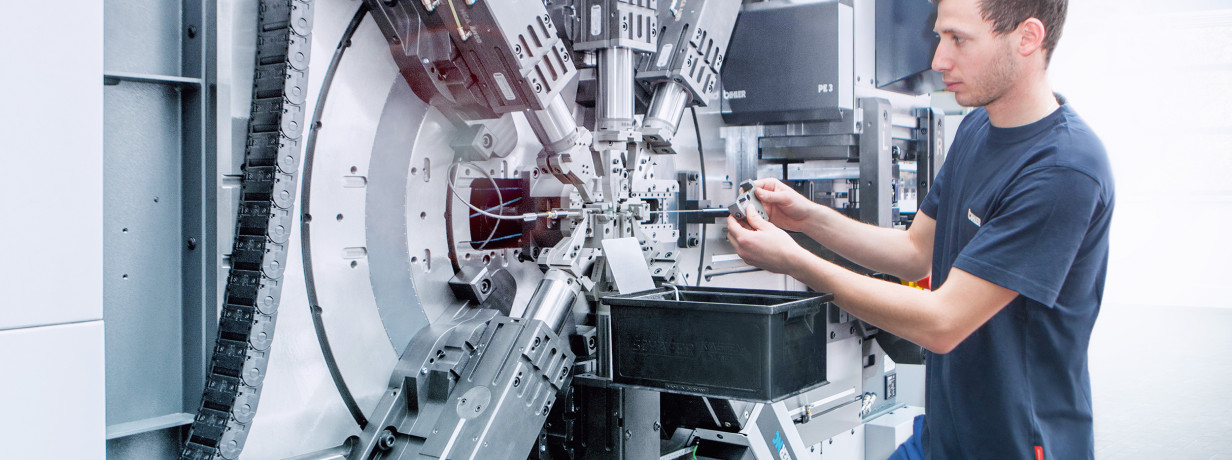
Balluff offers a broad range of sensors and position measurement systems using various technologies, all specially designed to meet the demands made on modern electrical, hydraulic and pneumatic drive systems.
You can choose from among a wide, flexible of existing solutions, or from our custom solutions designed to meet your needs and according to your individual specifications.
Significant benefits at a glance:
- Improved energy efficiency of machines and equipment
- Regulated machine sequences, controlled movements
For integration in linear and rotary drives: Compact, high-precision technology
Integrated sensor system solutions are indispensable for the most compact drive possible. BML magnetic encoders, which are available in incomparably small form factors, are suited for direct integration into both linear and rotary drives.
These measuring systems consist of a sensor and a magnetic tape, which features Permagnet technology for an absolutely homogeneous magnetic field. This guarantees high function security, low hysteresis and minimum linearity deviations.
During use, the sensor slides over the encoded tape at a distance of up to 5 mm for completely non-contact operation. The position is available as an absolute or incremental signal.
The tape is available as a strip for linear operations and in ring or disc form for rotary movement.
For additional flexibility you can choose from various interfaces (SSI, BISS-C, SIN/COS, ABZ, IO-Link).
Feedback systems for linear direct drives: High energy efficiency and drive quality since the system is highly precise and dynamic
The highly accurate and dynamic BML position measuring systems from Balluff ensure high energy efficiency and drive quality. The real-time capable measuring systems provide you with optimal position feedback at the highest energy efficiency for the best feedback quality – even in high-dynamic applications with traverse speeds of 10 m/s. The resolution of 1 µm means accuracy classes of up to ± 7 µm can be achieved.
Position feedback in the torque motor: Flat styles for large hollow shafts
When you're dealing with highly dynamic, fast and accurate positioning tasks, torque motors with BML magnetic encoder angle measurement systems are the ideal choice.
Used with a servo they ensure exact position feedback. This is critical for positioning accuracy, energy efficiency, life expectancy and the design of the entire application. Their small sensor head and flat code disc with large inside diameter make the Permagnet coded systems excellent for integration in torque motors.
Optimal control quality: high-precision measuring result
Consistently high positioning accuracy: play- and hysteresis-free
Flat drive: flat code disc
With SIN-/COS and ABZ interface
Detect end and intermediate positions with ease: Comprehensive portfolio of mini sensors for ideal solutions
For detecting end and reference positions, binary sensors ensure you of reliably simple position detection. With their compact sizes and low weight, our miniature series stands out from the many other options with its minimal space requirements and compatibility with moving actuators and slides. They are ideal, for example on grippers, gantry loaders or in pick-and-place applications, where every ounce of weight saved increases the energy efficiency of the system.
Whether directly in the drive or on various shafts of a packaging machine, rotational speeds are detected everywhere in machine and systems building. To measure rotational speeds and detect rotational direction and stops, we provide you with an optimal solution to meet your requirements. For simple checking you can often get by with one, but for simultaneous rotation direction sensing, two inductive standard sensors are needed.
For demanding use at higher speeds or precise speed determination, our angle measurement systems with magnetically-encoded rings are an optimal choice.
Digitizing the clamping process in the motor spindle: Monitoring tool clamping distance
Intelligent drive and clamping solutions where the sensors is integrated into the motor spindle are becoming increasingly common as an innovation driver on machine tools. The sensors needed for fast, smooth tool changes are available in ever smaller and more intelligent variations. These can be easily integrated into the clamping technology, regardless of whether it is activated electrically, hydraulically or pneumatically. With sensors and position measuring systems from Balluff you monitor the clamping and releasing process of the tools directly in the motor spindle.
Using the clever combination of pressure sensors or diverse redundant linear measurement systems based on different technologies, you can realize an enhanced safety level for the entire system.
Digitizing the motor spindle with IO-Link
Using the new IO-Link sensor and measuring systems you can easily incorporate the clamping technology for the motor spindle into the controller or digital network and digitize the motor spindle. This is accomplished using the open IO-Link standard, which enables fieldbus-neutral communication from the sensor/actuator level to the infrastructure of the Industrial Internet of Things (IIoT).
The future-oriented IO-Link technology makes your motor spindle more intelligent and ready for digitizing and the IIoT.