30.10.2023
Condition Monitoring Sensor BCM Generation 2
Smart condition monitoring on a new level
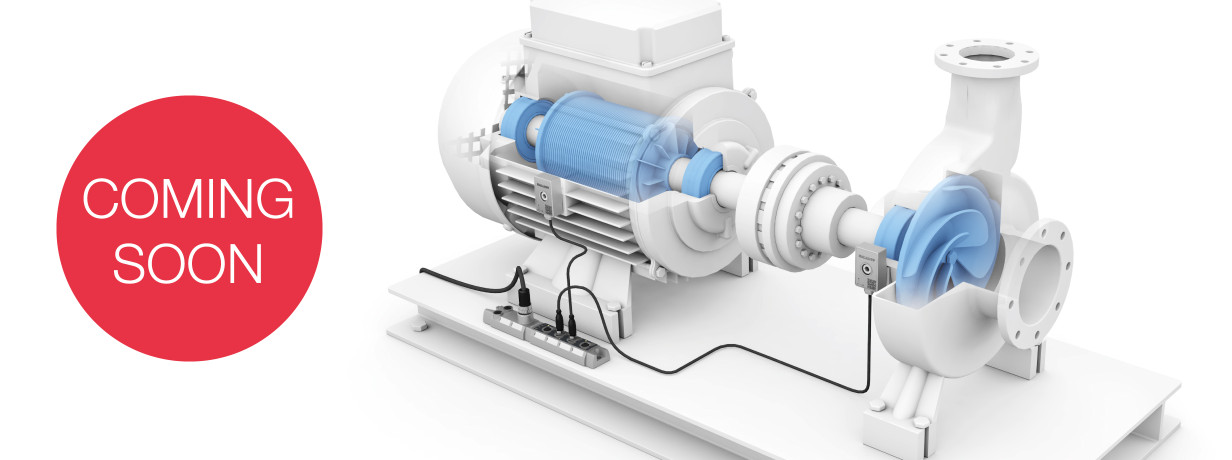
A standardized IO-Link interface combined with integrated intelligent data pre-processing: The new generation of the popular Condition Monitor Sensor BCM now sets another milestone in the field of smart IO-Link sensor technology.
From condition monitoring of critical components and assemblies to the detection of critical process states to the detection of relevant process parameters for inline process optimization: With the BCM Generation 2 you solve your condition monitoring applications in an optimal way.
Upgrade instead of update
The new condition monitoring sensor is not an iterative further development of the first generation, but a completely new platform with different hardware as well as firmware. The significantly improved measurement performance in combination with more sophisticated algorithms allow the sensor to detect the smallest condition changes even earlier and more specifically than before. Thanks to the new, convenient mounting concept with just one screw, it is also even easier to install.
In short: Compared to the first generation, the new BCM scores with a significantly higher performance level, intelligent algorithms and a sophisticated and efficient mounting concept.
Application data: intelligent - integrated
Thanks to integrated data pre-processing, lean, cost-effective condition monitoring systems can be set up and applications solved that previously required additional high-end evaluation units. In short: data volumes can be reduced to the essentials and unnecessary data traffic is avoided.
The BCM Generation 2 variants soon to be available from Balluff differ primarily in the degree of integrated data pre-processing, so you are guaranteed to find the right sensor for your application.
The special features
- smart condition monitoring sensor with standardized IO-Link interface
- several measured variables in one device: vibration and temperature
- very high performance vibration measurement with a frequency range of up to 6 kHz in three measurement axes
- early and targeted detection of critical condition changes through integrated frequency analysis
- simple and efficient installation and retrofitting due to sophisticated mounting concept
- Sensor self-monitoring with Balluff Smart Automation and Monitoring System (SAMS)