Machine vision: 5 simple steps to choose the right camera
Explore how to choose the right camera for your application

Reading Time: 5 minutes
The machine vision and industrial camera market is offering thousands of models with different resolutions, sizes, speeds, colors, interfaces, prices, etc. So, how do you choose? Let’s go through 5 simple steps which will ensure easy selection of the right camera for your application.
Defined task: Color or monochrome camera
Amount of information: Minimum of pixels per object details
Sensor resolution: Formula for calculating the image sensor
Shutter technology: Moving or static object
Interfaces and camera selector: Lets pick the right model
Step 1 – Defined task
It is always necessary to start with the size of the scanned object (X, Y), or you can determine the smallest possible value (d) that you want to distinguish with the camera.
For easier explanation, you can choose the option of solving the measurement task. However, the basic functionality can be used for any other applications.
In the task, the distance (D) between the centers of both holes is determined with the measurement accuracy (d). Using these values, we then determine the parameter for selecting the right image sensor and camera.
Example: Distance (D) between 2 points with measuring accuracy (d) of 0.05 mm. Object size X = 48 mm (monochrome sensor, because color is not relevant here)
Note: Monochrome or color?
Color sensors use a Bayer color filter, which allows only one basic color to reach each pixel. The missing colors are determined using interpolation of the neighboring pixels. Monochrome sensors are twice as light sensitive as color sensors and lead to a sharper image by acquiring more details within the same number of pixels. For this reason, monochrome sensors are recommended if no color information is needed.
Step 2 – Amount of information
Each type of application needs a different size of information to solve. This is differentiated by the minimum number of pixels. Let's again use monochrome options.
Minimum of pixels per object details:
Object detail measuring / detection: 3
Barcode line width: 2
Datamatrix code module width: 4
OCR character height: 16
Example: The measuring needs 3 pixels for the necessary accuracy (object detail size d). As necessary accuracy (d) which is 0.05 mm in this example, is imaged on 3 pixels.
Note: Each characteristic or application type presupposes a minimum number of pixels. It avoids the loss of information through sampling blurs.
Step 3 – Sensor resolution
We already defined the object size as well as resolution accuracy. As a next step, we are going to define resolution of the camera. It is simple formula to calculate the image sensor.
S = (N x O) / d = (min. number of pixels per object detail x object size) / object detail size
Object size (O) can be describe horizontally as well as vertically. Some of sensors are square and this problem is eliminated 😊
Example: S = (3 x 48 mm) / 0.05 mm = 2880 pixels
We looked at the available image sensors and the closest is a model with resolution 3092 x 2080 => 6.4 megapixel image sensor.
Note: Pay attention to the format of the sensor.
For a correct calculation, it is necessary to check the resolution, not only in the horizontal but also in the vertical axis.
Step 4 – Shutter technology
Global shutter versus rolling shutter.
These technologies are standard in machine vision and you are able to find hundreds of cameras with both.
Rolling shutter: Exposes the motive line-by-line. This procedure results in a time delay for each acquired line. Thus, moving objects are displayed blurrily in the resulting motive through the generated “object time offset” (compare to the image).
Pros:
More light sensitive
Less expensive
Smaller pixel size provides higher resolution with the same image format.
Cons: Image distortion occurs on moving objects
Global shutter: Used to get distortion-free images by exposing all pixels at the same time.
Pros: Great for fast processes, sharp images with no blur on moving objects.
Cons:
More expensive
Larger image format
Note: The newest rolling shutter sensors have a feature called global reset mode, which starts the exposure of all rows simultaneously and the reset of each row is released simultaneously, also. However, the readout of the lines is equal to the readout of the rolling shutter: line by line.
This means the bottom lines of the sensor will be exposed to light longer! For this reason, this mode will only make sense, if there is no extraneous light and the flash duration is shorter or equal to the exposure time.
Step 5 – Interfaces and camera selector
Final step is here:
You must consider the possible speed (bandwidth) as well as cable length of camera technology.
USB2
Small, handy and cost-effective, USB 2.0 industrial cameras have become integral parts in the area of medicine and microscopy. You can get a wide range of different variants, including with or without housings, as board-level or single-board, or with or without digital I/Os.
USB3/GigE Vision
Without standards every manufacturer does their own thing and many advantages customers learned to love with the GigE Vision standard would be lost. Like GigE Vision, USB3 Vision also defines:
A transport layer, which controls the detection of a device (Device Detection)
The configuration (Register Access)
The data streaming (Streaming Data)
The handling of events (Event Handling)
Established interface to GenICam.
GenICam abstracts the access to the camera features for the user. The features are standardized (name and behavior) by the standard feature naming convention (SFNC). Additionally, it is possible to create specific features in addition to the SFNC to differentiate from other vendors (quality of implementation). In contrast to GigE Vision, this time the mechanics (e.g. lockable cable connectors) are part of the standard which leads to a more robust interface.
I believe that these five points will help you choose the most suitable camera. Are you still unclear? Do not hesitate to contact us or contact me directly: I will be happy to consult your project, needs or any questions.
Keywords
- Machine vision
Author
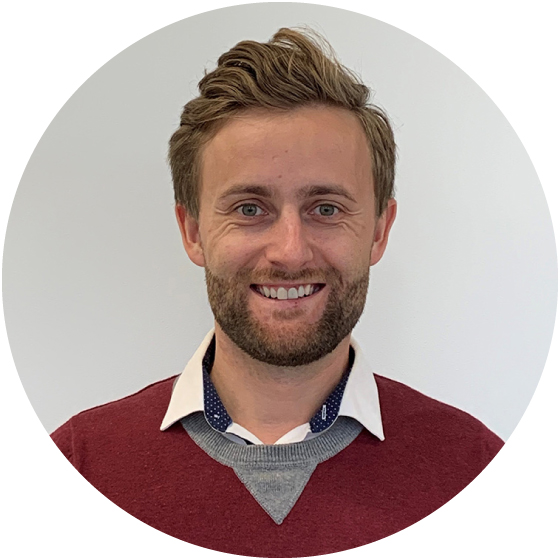
František Jakubec
11 Contributions
Comment
Popular posts
Industrial sensing fundamentals – NPN vs PNP
What is a capacitive sensor?
How do I wire my 3-wire sensors?
The basic operating principle of an inductive proximity sensor
Contact form
Do you have any questions or suggestions? We are at your disposal.
Balluff Inc.
-
8125 Holton Dr.
Florence, KY 41042